For Dean Carpenter, a cabochon is not a difficult word to pronounce and is part of an easy hobby to get hooked on. Creating the highly polished, convex-cut, unfaceted gemstones has been a lifelong interest, one insiders call “cabbing.”
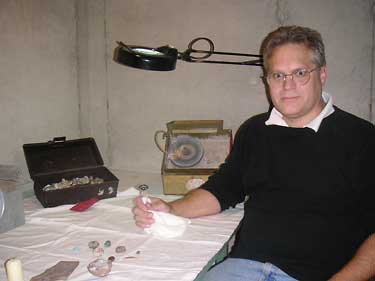
“It’s interesting to find the optimum presentation of the stone,” Carpenter says. “That’s where most of the work in cabbing comes from—to cut the stone in such a way that it finds its best face. Believe me, I’ve ruined enough stones doing it wrong, but if you do it in the right way it will really show a unique pattern and color.”
Carpenter says he does not think many people have heard of the rounded gemstones, adding that it catches his eye when people have a stone that has been cabbed. He says belt buckles are one accessory that often feature cabochons.
A registered nurse at the Cardiology Stepdown Unit, Carpenter first took up the craft when he was in middle school. He says his father signed him up for a class and he instantly was hooked. Carpenter says cabbing allows him to take time away from the demands of caring for very ill patients at the hospital.
“You get into sort of a Zen-like place just looking at the stone,” says Carpenter, who currently is working on an unfinished Lake Superior agate. Carpenter says he enjoys working with several stones: agates, which have a lot of color and variation; tiger-eye; and the Isle Royale green stone, the official gemstone of Michigan.
Cabbing is a detailed process, Carpenter says. He buys his stones from a gem shop so they already are cut into very thin strips by a slab saw.
“It’s a large saw with a diamond encrusted blade like a meat cutter at a deli,” Carpenter says. The slab saw cuts thin slices of a larger stone. “The idea is to get a flat stone that’s at the most maybe a half an inch thick.”
Carpenter continues the process using a trim saw in the workshop in his garage at home to trim out the rough shape, usually an oval, he says. He then attaches the stone to a wooden dowel with heated jeweler’s wax. The wax hardens, holding the stone to the dowel.
While the stone is attached, Carpenter grinds the edges and continues to round the borders of the gem. He uses sand paper and a polishing compound to complete the process. Finally, the stone is ready for a setting.
From the initial slab to the finished product, the process takes about 2-3 hours, he says.
Carpenter creates cabochons as gifts for friends and family. At times he makes gifts with a specific person in mind, like the present he crafted for his wife, Rhonda. On a hiking trip Carpenter took to Isle Royale with his sons, Kyle and Evan, he collected stones and took them back to his workshop, where he created earrings.
When he was 13, Carpenter made an entire set of jewelry out of snowflake obsidian, black with white flecks, as a birthday gift for his grandmother. A necklace with a pendant, broach and earrings completed the set.
These days, Carpenter teaches his children and their friends how to make cabochons.
“I think it would be a fun hobby for young people to learn,” Carpenter says.